Sensorless Field Oriented Control of PMSM
Field-oriented control of PMSM has become widespread since it allows you to quickly, smoothly, and accurately control the position of the shaft, speed, and torque of the electric motor. But to implement this control method, it is necessary to know the position of the rotor.
- According to the method for determining the rotor position of an electric motor, two methods of field-oriented control are distinguished:
- sensor - feedback on the position sensor and/or speed sensor;
- sensorless - information about the rotor position is calculated mathematically in real-time based on the information available in the control system.
The application of one or another method of field-oriented control is determined by the application field of the electric drive. For small ranges of speed variation (no more than 1:100) and requirements for the accuracy of its maintenance no more than ± 0.5%, sensorless vector control of the electric motor is used. If the shaft rotation speed varies over a wide range (up to 1:10000 and more), there are requirements for high accuracy of maintaining the rotation speed (up to ± 0.02% at rotation frequencies less than 1 Hz) or there is a need to position the shaft, and if necessary of the torque control on the shaft of the electric motor at very low speeds, is used the methods of vector control with speed feedback [1].
- The problem of sensorless control of a permanent magnet electric motor can be divided into 3 stages:
- determining the initial position of the rotor for starting the electric motor;
- control of the electric motor at low speeds, i.e. acceleration of the electric motor to speed (usually 10% of the nominal), where the generated back-EMF becomes sufficient to determine the position of the rotor;
- acceleration of the electric motor to the rated (preset) rotation speed, control of the motor rotation speed during operation, maintaining the maximum torque.
Sensorless start
The task of correctly starting a synchronous electric motor is one of the main tasks in modern control systems. To do this, you need to know the exact position of the rotor. In the case when there is no absolute position sensor, the simplest solution is to apply voltage to one of the phases and wait until the rotor is oriented along the field. But in the event that the position of the rotor poles does not coincide with this phase, the rotor can make an uncontrolled backward movement, and if the rotor has only one pair of poles (these are most often used on high-speed electric motors) and not take the required position at all.
Since the rotor of an electric machine at the initial moment is in a stationary state, it does not create a back EMF, which makes it possible to determine its position, therefore all methods for determining the initial position of the rotor is using a special test signal that is fed to the stator of the motor, and a special algorithm for analyzing the response to it.
- There are the following methods of sensorless determination of the initial position of the rotor:
- carrier signal injection;
- PWM method;
- the current impulse method [2].
Since only the third method allows determining the position of the rotor and distinguishing the north pole from the south pole, it is optimal for solving the problem of sensorless start. The approach is based on the study of changes in the inductance of the stator coils depending on the position of the rotor. It involves applying the correct sequence of voltage pulses applied to the stator coils and measuring the peak value of the currents received to estimate the position of the rotor.
The time to determine the initial position without a sensor takes less than 15 ms.
Sensorless motor control
At low speed
At low speed (0-10% of rated speed), the back EMF generated by the motor is insufficient to determine the position of the rotating rotor. Therefore, information about the position of the rotor is obtained due to the difference between the inductances along the d and q axes, which is available in the PMSM with a salient poles rotor. For this, a high-frequency component is superimposed on the main control signal (the signal is modulated). After that, a high-frequency component is allocated, from which information about the position of the rotor and the speed of rotation of the electric motor is extracted.
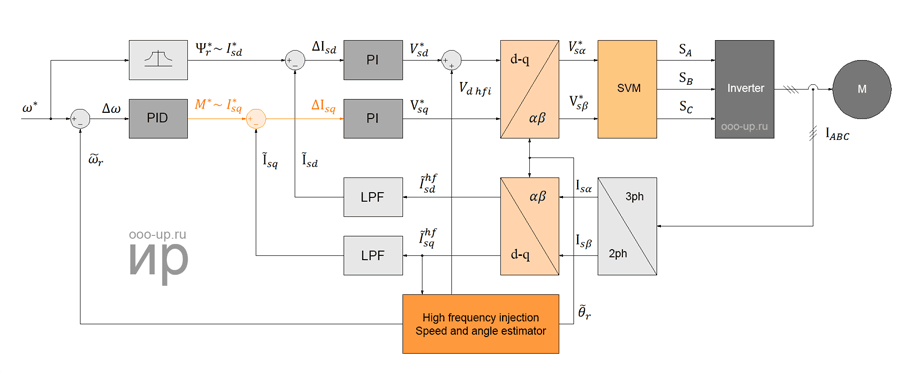
At the work speed
By the work speed range (10% - 100% of the rated rotation speed), we mean such a mode of operation when the speed of the electric drive is sufficient for the back EMF level to be sufficient to calculate the rotor position with acceptable accuracy. To calculate the angle, a state observer is used, which implements the calculation of all the variables and parameters of the permanent magnet motor required to implement the adaptive vector control algorithm, based on information about two stator phase currents (taken from current sensors) and two specified phase voltages.
High speed solutions
In applications such as centrifugal compressors and turbomolecular pumps are required high-speed electric motors with a rotation speed of more than 60,000 rpm. For this, permanent magnet synchronous motors are used, the rotor of which has one pair of poles. Since the rotor position sensor at high speeds has a high error and it is not always possible to make it constructively, such applications require the use of sensorless control systems.
- This task for electric motor control is also divided into several stages:
- sensorless determination of the initial position;
- scalar start;
- vector control at high speeds (in case of changing load).
- Modern frequency converters: control methods and hardware implementation [Ru]
- Jan Persson. Innovative standstill position detection combined with sensorless control of synchronous motors.- Lausanne, Switzerland.: École polytechnique fédérale de Lausanne (EPFL), 2005.
- Peter Vas. Sensorless vector and direct torque control.- Oxford, UK.: Oxford University Press, 1998.
- Dianov A.N. Development and research of a sensorless brushless motor control system. - Moscow: Moscow Power Engineering Institute, 2004.
- Bon-Ho Bae, Seung-Ki Sul, Jeong-Hyeck Kwon and Jong-Sub Shin. Implementation of sensorless vector control for super-high speed PMSM of turbo-compressor.- Seoul, Korea.: Samsung Techwin Co., ltd, 2001
- Christof Zwyssig, Johann W. Kolar, and Simon D. Round. Megaspeed drive systems: pushing beyond 1 million r/min.- Zurich, Switzerland.: Swiss Federal Institute of Technology (ETH), 2009.
References
Also read
-
Hysteresis motor
Construction, principle of operation, advantages, and disadvantages of a hysteresis motor
-
Synchronous reluctance motor
Construction, working principle, and features of a synchronous reluctance motor
-
Scalar control
The principle of operation of the scalar (frequency) control is to maintain a constant voltage/frequency ratio over the full operating speed range
-
Vector control
Vector control allows you to independently control the speed and torque of the electric motor. The main idea of vector control is to control not only the magnitude and frequency of the supply voltage but also the phase