Scalar control of motor
The V/Hz ratio is calculated based on the rated values (voltage and frequency) of the controlled AC motor. By keeping the value of the V/Hz ratio constant, we can maintain a relatively constant magnetic flux in the motor gap. If the V/Hz ratio increases, then the motor becomes overexcited and vice versa if the ratio decreases the motor is in an unexcited state.
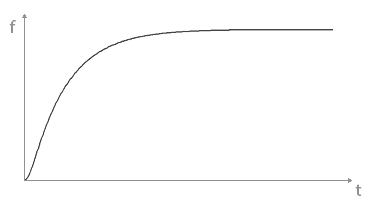
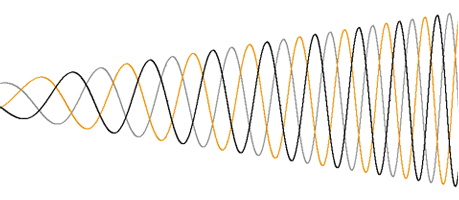
At low speed, it is necessary to compensate the voltage drop across the stator resistance, therefore, the V/Hz ratio at low speed is set higher than the rated value. The scalar control technique is most widely used to control induction electric motors.
As applied to induction motors
At the scalar control method, the induction motor speed is controlled by setting the voltage and frequency of the stator, so that the magnetic field in the gap is maintained at the desired value. To maintain a constant magnetic field in the gap, the V/Hz ratio must be constant at different speeds.
As the speed increases, the stator supply voltage must also increase proportionally. However, the synchronous speed (frequency) of the induction motor is not equal to the rotation speed (frequency) of the shaft, and the slip of the induction motor depends on the load. Thus, the controller with scalar control without feedback cannot accurately control the speed when there is a load. To solve this problem, speed feedback and, therefore, slip compensation can be added to the control system [2].
When used
Scalar control of AC motors is a good alternative for applications where there is no variable load and no good dynamics (fans, pumps) are required. The scalar control does not require a rotor position sensor, and the rotor speed can be estimated from the frequency of the supply voltage. When scalar control is used, a high-performance digital signal processor is not required, as is the case with vector control.
Disadvantages of scalar control
With scalar motor control, the stator currents are not directly controlled.
PMSM with scalar control can easily become uncontrollable (get out of the synchronous state) especially when the load torque exceeds the value of the drive torque limit value. The scalar method is not suitable for the control of PMSM at low speed for applications requiring high dynamics [1].
- The scalar control technique is relatively simple to implement, but has several significant drawbacks:
- if the speed sensor is not installed, the rotation speed of the induction motor shaft cannot be controlled, since it depends on the load (the presence of a speed sensor solves this problem), and in the case of a synchronous motor, when the load is changed, you can completely lose control;
- the torque cannot be controlled. Of course, this task can be solved with the help of a torque sensor, but the cost of its installation is very high, and will most likely be higher than the electric drive itself. In this case, the torque control will be very inertial;
- you can't control torque and speed at the same time.
Scalar control is sufficient for most tasks in which an electric drive is used with a range of motor speed control up to 1:10.
When maximum performance is required, the ability to control over a wide speed range and the ability to control the torque of the motor are used vector control.
Also read
-
Synchronous reluctance motor
Construction, working principle, and features of a synchronous reluctance motor
-
Brushed DC motor
The construction, types, working principle and main parameters of the brushed DC motor
-
Vector control
Vector control allows you to independently control the speed and torque of the electric motor. The main idea of vector control is to control not only the magnitude and frequency of the supply voltage but also the phase
-
Sensorless FOC of PMSM
Sensorless vector control of permanent magnet synchronous motors. Control method for high-speed electric motors